Why, When and How to Replace Lathe Oils, Lubricants and Coolants
The squeaky wheel gets the grease is a common saying that should never apply to your lathe and its lubricants. The slides, apron, chucks, mandrels, bearings and spindles should never get to that point. Any machine shop’s pre-operation checklist should include evaluations of all the fluids and lubrication levels to avoid catastrophic failure. New LeBlond lathes make it easy to identify the fluid levels and top off the lathe lubrication reservoirs to keep everything running smoothly.
It may seem obvious why you should replace the lubrication fluids regularly, but different lubrication and cooling oils have specific purposes and benefits. The best oil or lubricant can depend on the machine component, material cut, or tool used. The lubrication used to maintain smooth operation of the machine is different than the coolants used to cut billets. Metal cutting fluids help minimize heat transfer and fluctuation, reduce friction, and manage chips that may otherwise do damage.
There are three main types of machine-cutting fluids:
- Soluble Oils–These oils are emulsified and mixed with water. These water-soluble lubricants are prone to grow fungus and bacteria if the pumps aren’t maintained. This is the least expensive and most used type of cutting fluid.
- Synthetic fluids–These fluids replicate natural oil lubrication but are made of polymers and chemicals. They prevent corrosion, are the cleanest and offer best cooling of the different lubricants. However, they are the least lubricant.
- Semisynthetic fluids–use a combination of both soluble and synthetic fluids. The heat transfer performance is somewhere between soluble and synthetic fluids. These lubricants have a broad range of applications.
One thing universal for lathe lubrication is to select a non-detergent oil. Oils with detergent attract and collect particles and chips as the metal is machined.
So, how do you know when to replace the lubricants? Depending on the lathe, you may need to either manually lubricate or this function can be automatic:
LeBlond Precision High-Speed Lathes (RKL-1300, 1500, 1700 and 1900) as well as Precision High-Speed Heavy-Duty Lathes (RKL-1600, 1800 and 2000) have a manual, one-shot handpump on the apron. It’s recommended that an operator use the manual lubrication three times per day during normal operation. Additionally, the cross slide is lubricated by oil fittings, which are lubricated by an oil can. LeBlond recommends 2-3 drops of oil to each fitting daily or as needed.
LeBlond Heavy Duty Lathes (RKL-2100, 2500 and 2900) have an auto lubrication system. It is recommended to keep the lubrication setting for the cross slide and longitude apron at 1/8” to avoid flooding the whole system, lose oil too quickly and refill lubricant more than needed. By keeping the setting at 1/8”, the lathe will typically have enough oil for an 8-hour shift. Of course, this depends on all variables: lathe speed, metal type and particular operations. At the beginning of every shift, it is important to check the head stock, apron and bedway lubrication levels are full. Whenever the carriage kicks into gear, the built-in self-lubricating pump activates. This lubrication pump can be turned off for specific operations (like cutting titanium, cast iron or other hardened steel alloys), but it is recommended to keep the pump on and set to 1/8” to maintain a sufficient flow of lubricants.
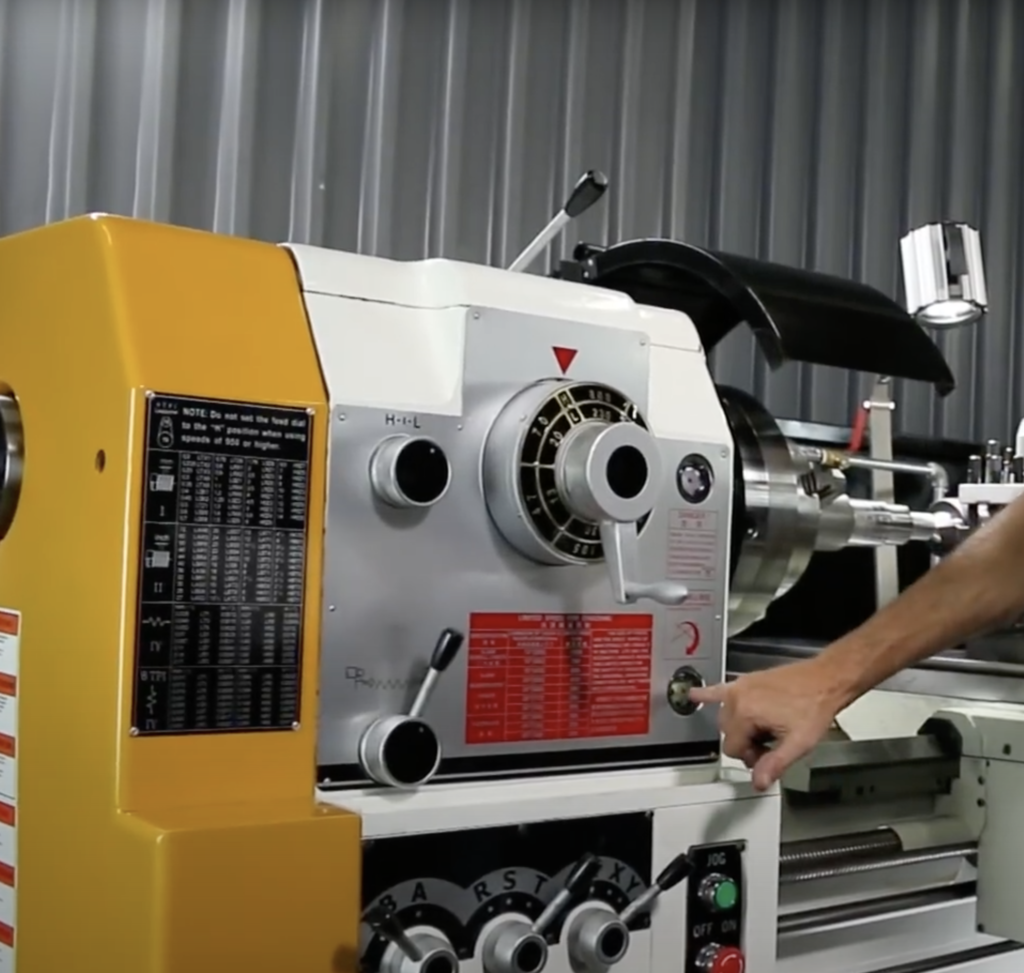
The first of three windows to view oil/lubricant levels on the RKL Heavy Duty Lathe
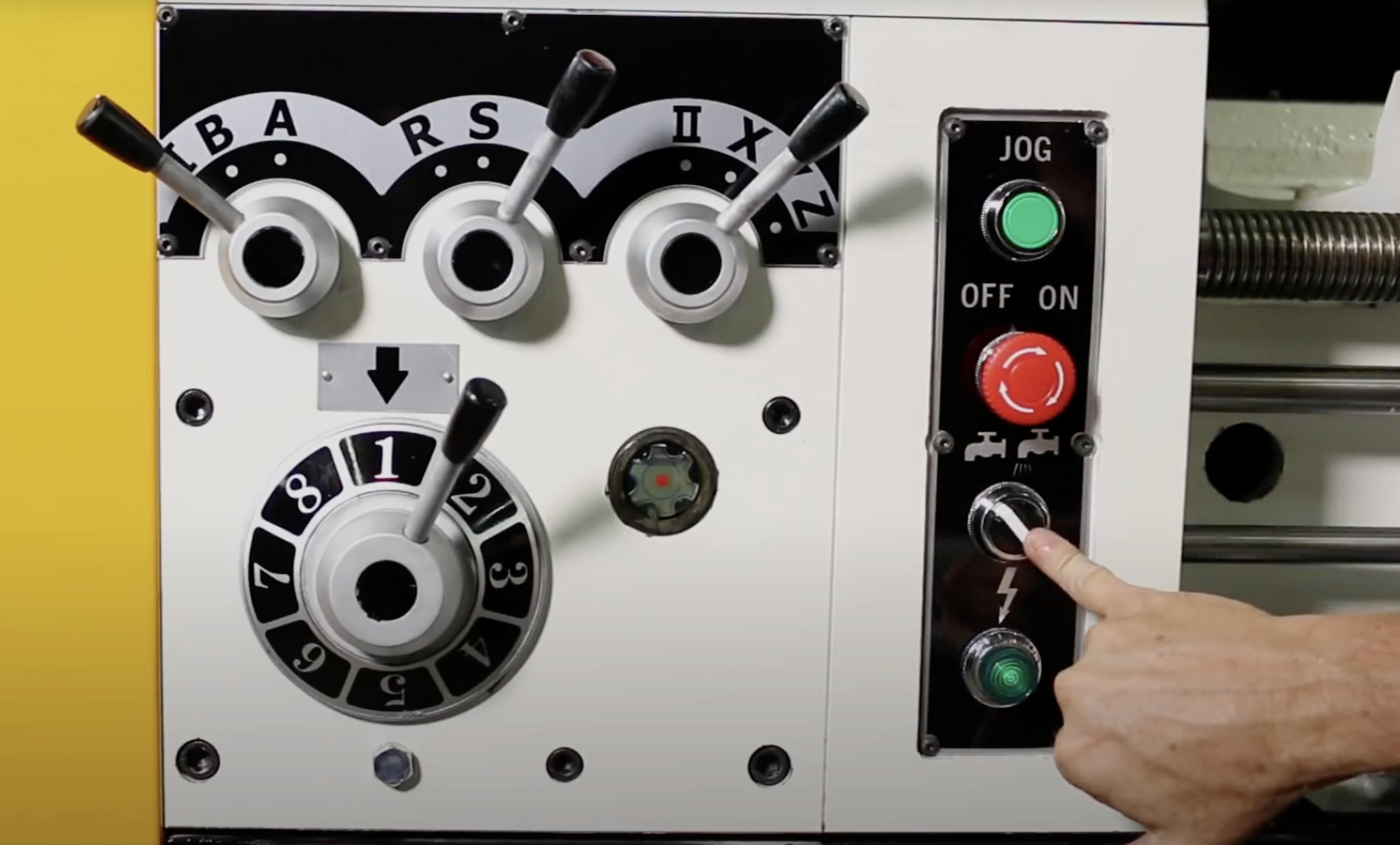
On & off switch for coolant
There are 3 auto lubrication settings on the slide and apron longitude:
- B = Bedway
- C = Cross slide apron longitude
- BC = lubricates both
The lathe operator can adjust these settings as needed.
Additionally, it is important to check all other lubrication points prior to running the lathe to assure smooth functionality. Maintaining a reliable operation of the lathe requires keeping the necessary spindles, slides, gears and bearings oiled regularly.
There are many ways to check a lathe’s lubrication levels to maintain the best operation. Regular lubrication is vital for extending the life of a LeBlond lathe. When the saying, “Running like a well-oiled machine,” was coined, they had LeBlond lathes in mind.
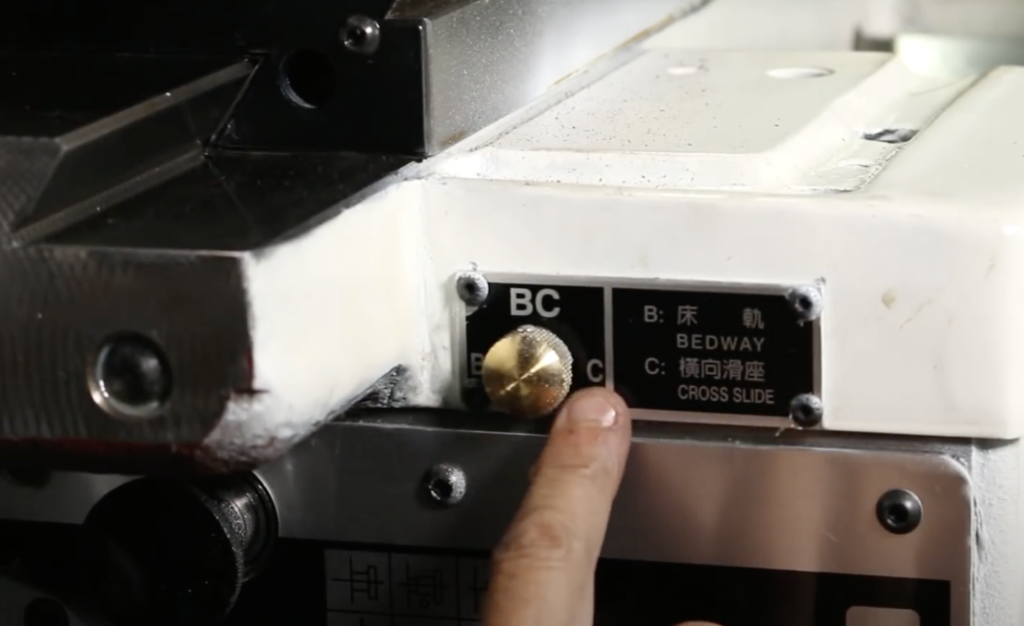
Lubrication knob adjusts whether to send lubricants to the cross slide, the bedway, or both.