4 Essential Tips for Professional Machinists
In the past, it would take years as a journeyman to master a discipline. However, machine shop machinists can master chip control with four essential tips. In high-precision machining, chip control is far more than a matter of cleanliness — it’s central to productivity, tool life, surface finish, and shop safety. Here’s a breakdown of four critical elements that every professional machinist should understand and implement.
1. Tool Geometry Directly Influences Chip Formation
Tool geometry — especially rake angle, nose radius, and chip breaker design — plays a pivotal role in how chips are formed and evacuated. A chip breaker is a specially designed feature on a cutting tool — often a groove, step, or raised geometry — that controls the flow and shape of metal chips as they’re formed during machining. It plays a critical role in breaking chips into smaller, more manageable pieces rather than allowing long, stringy ones that can damage tools, surfaces, or even pose safety risks.
For example, a positive rake angle (typically +10° to +20°) facilitates cleaner chip formation in softer materials like aluminum, reducing power consumption and heat. Conversely, negative rake angles are more durable and used in harder materials, but they produce thicker, more curled chips. Using inserts like the ISO CNMG or DNMG with built-in chip breakers tailored to material types enhances chip segmentation, improving control and evacuation. In short: a chip breaker is like a traffic engineer for metal chips — guiding and forcing them into manageable paths to improve tool life, part quality, and shop safety.
2. Cutting Parameters Must Be Tuned for Chip Flow
Feed rate, speed, and depth of cut need to align with both material and tooling. For instance, in turning 4140 steel at 220 Brinell, recommended settings using a CVD-coated carbide insert might be:
- Vc (cutting speed): 180–240 m/min
- Feed rate: 0.2–0.4 mm/rev
- Depth of cut: 1.5–3.0 mm
Exceeding or falling short of these ranges can cause stringy chips or erratic flow, which in turn affects tool wear and finish quality.
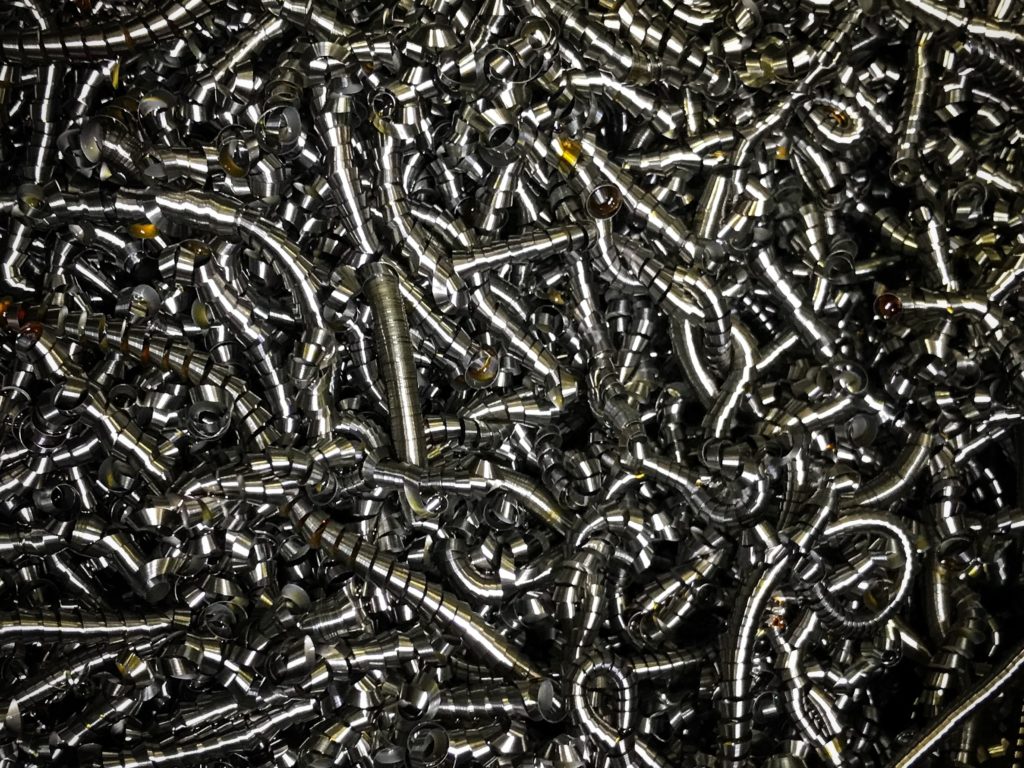
3. Coolant Strategy Affects Chip Breakage and Evacuation
High-pressure coolant (HPC), often around 1000–2200 PSI, improves chip control in deep-hole drilling and turning by breaking chips early and aiding evacuation. Systems like through-tool coolant delivery ensure the fluid reaches the cutting zone precisely, preventing chip welding or re-cutting. Read more about coolants in our coolant blog.
4. Material Type Dictates Chip Behavior
Different alloys require tailored chip control strategies. For example, austenitic stainless steels (e.g., 316L) tend to form long, ductile chips — here, sharper tools with aggressive chip breakers and adequate coolant are vital. In contrast, gray cast iron, being brittle, naturally forms short chips, requiring less intervention but more dust management.
Understanding and refining chip control leads to better part finishes, longer tool life, and safer workspaces. In competitive shops, it’s the difference between average and elite machining. Now that you have mastered these tips, you will be prepared for more complex machining challenges.