Evaluating Your Practices Can Cut Machining Costs
Saving time, improving efficiencies, reducing waste are all ways to cut machining costs and increase margins for machining parts. However, putting the right tactics in place to achieve these cost cutting measures is easier said than done. Below are some practical tips to cut costs when cutting parts.
Keep Cool
Excessive heat can cause tool wear, poor surface finish, dimensional inaccuracies and ultimately scrapped parts. Machinists can control heat generation to reduce the risk of tool wear and workpiece deformation. It’s important to use the appropriate water-based or oil-based coolant depending on the application. Cutting fluids should have good thermal stability to avoid breaking down at high temperatures as well as an appropriate viscosity to ensure proper flow and coverage.
Cutting lubricants can have different viscosities depending on the specific application and the type of cutting fluid used. Generally, cutting lubricants are classified into three viscosity ranges: low viscosity, medium viscosity, and high viscosity.
- Low viscosity lubricants have a viscosity range of 2-5 cSt (centistokes) and are used for high-speed machining operations such as drilling, tapping, and milling. Low viscosity lubricants provide good cooling and flushing properties and are suitable for operations where chip removal is important.
- Medium viscosity lubricants have a viscosity range of 5-20 cSt and are used for general machining operations such as turning, boring, and threading. Medium viscosity lubricants provide good lubrication and cooling properties and can help improve tool life.
- High viscosity lubricants have a viscosity range of 20-100 cSt and are used for heavy-duty machining operations such as broaching, gear cutting, and deep hole drilling. High viscosity lubricants provide excellent lubrication and cooling properties and are suitable for operations where high pressure and high temperatures are present.
In addition to these three viscosity ranges, cutting lubricants can also be formulated to have specific viscosities that are tailored to the specific application. For example, some cutting lubricants may have a viscosity of 10 cSt at room temperature but can increase to 50 cSt at the high temperatures generated during machining.
The choice of cutting lubricant viscosity will depend on the specific application and the cutting parameters used. Fluids that are too thick can cause problems with flow and coverage, while fluids that are too thin may not provide adequate lubrication and cooling. Machinists should consult with cutting fluid suppliers or a LeBlond representative for guidance on selecting the appropriate lubricant viscosity for the application.
Find the Right Cutting Forces
The cutting forces involved in lathe machining are typically measured in three directions: tangential, radial, and axial.
- The tangential force acts parallel to the workpiece surface and is responsible for the cutting action.
- The radial force acts perpendicular to the workpiece surface and is responsible for the tool deflection.
- The axial force acts along the lathe axis and is responsible for the tool wear.
The tool geometry is important to minimize heat transferred to a part. In addition to adjusting cutting parameters, machinists can also select cutting tools with appropriate geometries to optimize cutting forces. For example, tools with sharp cutting edges can reduce cutting forces and improve surface finish, while tools with larger nose radii can increase cutting forces and improve tool life. To optimize cutting forces, machinists can adjust cutting parameters such as cutting speed and depth of cut. Increasing cutting speed can increase cutting forces and remove material more efficiently, but may also increase tool wear and workpiece deformation. Decreasing cutting speed can reduce cutting forces, but may also result in lower productivity. Machinists must balance cutting forces with tool wear, workpiece deformation, and productivity to achieve effectively cut machining costs.
Let the Chips Fall
Watching the chips can give machinists a good indication of efficient production. The color of the chip can provide insight into the machining process. For example, a blue chip indicates high temperatures, while a silver or bronze chip indicates good cutting conditions. By monitoring chip color, operators can adjust cutting parameters to optimize the machining process. Next, thick chips indicate a slow feed rate. By adjusting the feed rate, operators can control chip thickness and improve efficiency. Third, the curl of the chip can provide information about the cutting conditions. A tight, continuous curl indicates a well-designed cutting tool, while a loose, discontinuous curl indicates poor cutting conditions. By monitoring chip curl, operators can adjust cutting parameters and optimize the machining process. Finally, the shape of the chip can provide information about the workpiece material and the cutting tool geometry. By analyzing chip shape, operators can adjust cutting parameters and select the appropriate cutting tool to optimize the machining process.
Evaluating the right cutting fluids, cutting forces and chip formations can give a good indication of the performance of the machining process. Finding the right balance of these measures can save time and waste. Cost savings occur when maintaining optimal conditions when machining parts on a lathe. For more ideas on how to cut machining costs for your manufacturing process, contact your LeBlond representative.
For cost saving machines, please submit a request through our online form or call (888) 532-5663 and select option 2.
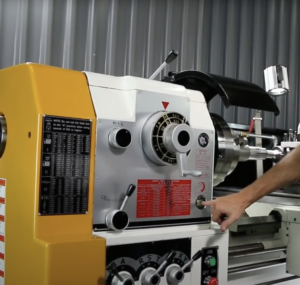