Five Habits Machinists Possess to Minimize Downtime
What you can do to optimize the production of machined parts.
Minimizing downtime is crucial for metalworking machinist to keep operations running smoothly and meet production targets. However, maintenance-related downtime remains a significant pain point, impacting productivity, timelines and costs. Here are some of the key solutions machinists use to minimize downtime.
1. Planned Maintenance During Off-Peak Hours
- Schedule planned downtime
Balancing maintenance schedules with production deadlines is difficult. While preventive maintenance helps avoid breakdowns, it still interrupts production. Perform maintenance during low-production periods, such as evenings, weekends, or planned plant shutdowns, when the impact on production will be minimal. - Coordinate with production schedules
Scheduling maintenance during low production periods or machine idle times is ideal but not always possible in high-demand environments, forcing machinists to navigate tight deadlines and pressure to reduce downtime. Align maintenance with the production team to ensure critical tasks are completed beforehand, reducing the likelihood of delaying important jobs.
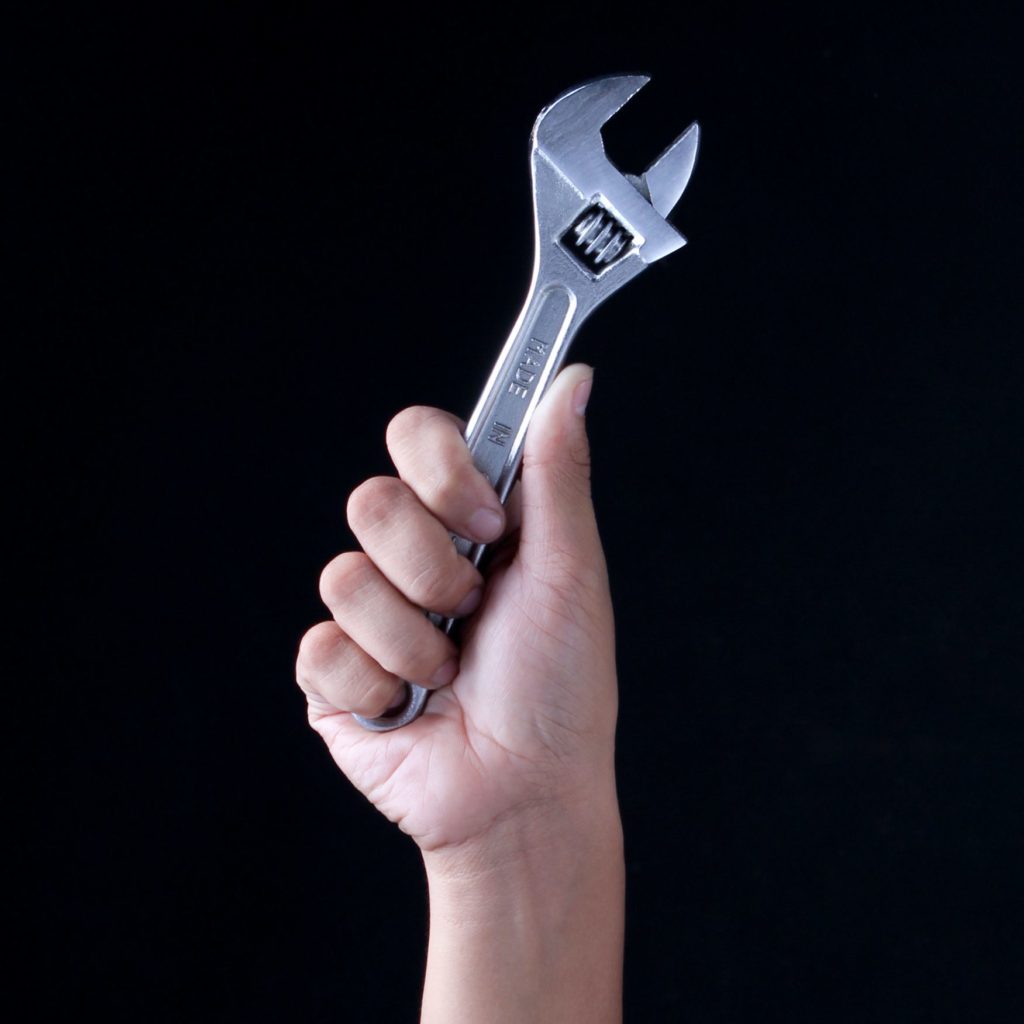
2. Plan a Detailed Maintenance Schedule
- Use preventive maintenance plans
Even scheduled maintenance can turn into extended downtime if repairs take longer than anticipated. Regularly scheduled maintenance prevents unexpected breakdowns. Keeping a log of maintenance intervals ensures that necessary tasks are completed on time. - Leverage machine monitoring systems
Predictive maintenance software can analyze machine usage and forecast when components are likely to fail, allowing for proactive scheduling before a problem arises.
3. Stock Spare Parts and Tools
- Store critical spare parts
Supply chain issues made sourcing vital spare components difficult. Keep an inventory of high-wear parts like belts, bearings, seals, and lubricants to avoid waiting for replacements. - Ensure tool readiness
Worn-out tools cause poor surface finishes, reduced accuracy, scrap and eventual machine damage if not replaced in time. Have any required special tools or calibration equipment on hand, reducing delays in maintenance.

4. Notify and Train Operators in Advance
- Pre-maintenance notifications
Inform operators and production managers well ahead of scheduled maintenance, so they can adjust their workloads or complete urgent jobs beforehand. - Train machine operators to minimize downtime
Ensure that operators are aware of basic maintenance tasks like lubrication, cleaning, and tool replacement, reducing the frequency of more extensive servicing.
5. Prepare Detailed Maintenance Checklists
- Use step-by-step checklists
Document a detailed maintenance checklist covering inspections, lubrication, part replacements, and calibrations. This ensures no critical tasks are overlooked and speeds up the process. - Log maintenance activities
After each scheduled maintenance, document all completed tasks and any issues encountered for future reference and improvement.
By implementing these strategies, machinists can better prepare for scheduled maintenance, keeping production disruptions to a minimum and ensuring machines stay reliable and efficient. To mitigate downtime pain points, machinists can benefit from predictive maintenance technologies, and better planning, all of which reduce unplanned downtime and extend machine lifespan. Minimizing downtime by investing in better maintenance strategies ultimately leads to higher uptime, reduced costs, and a more efficient shop floor.