How to stay sharp and be cool.
You wouldn’t shave with a dull razor or cut a steak with a butter knife, right? The same goes for machining—keeping your tools sharp and effective is the key to a clean, efficient cut. Whether you’re a seasoned machinist or just getting your hands dirty in the shop, understanding the right machine tool inserts and coatings can make all the difference. Let’s break it down so you can cut with confidence.
Choosing the Right Material for Your Inserts
Machine tool inserts come in different materials, each suited to specific applications. Picking the right one means better performance, longer tool life, and, of course, less frustration on the shop floor.
- Carbide Inserts: The workhorse of the machining world, carbide inserts are most common, durable, heat-resistant, and suitable for most materials. They offer a great balance between cost and performance.
- Ceramic Inserts: Need to crank up the speed? Ceramic inserts handle high temperatures and are perfect for high-speed machining of hard materials.
- CBN (Cubic Boron Nitride): When you’re working with hardened steels, CBN inserts shine. They maintain cutting edge integrity even under extreme conditions.
- PCD (Polycrystalline Diamond): If you’re cutting non-ferrous materials or composites, PCD inserts provide superior wear resistance and precision.
- High-Speed Steel (HSS): While not as flashy as the others, HSS is still a solid choice for low-speed operations that require detailed work and precision.
The Power of Coatings
Selecting the right insert material is only half the battle—coatings give your tools the extra edge (literally) to last longer and perform better. Here are some of the most popular options:
- TiN (Titanium Nitride): A classic gold-colored coating that reduces friction and enhances wear resistance, extending tool life significantly.
- TiAlN (Titanium Aluminum Nitride): Ideal for high-temperature applications and dry cutting, this coating is built for the heat.
- ZrN (Zirconium Nitride): Perfect for improving chip flow and corrosion resistance, making it great for machining aluminum and other sticky materials.
- Diamond Coating: If you’re working with non-ferrous materials or abrasive applications, diamond-coated inserts are your best bet for extreme durability.
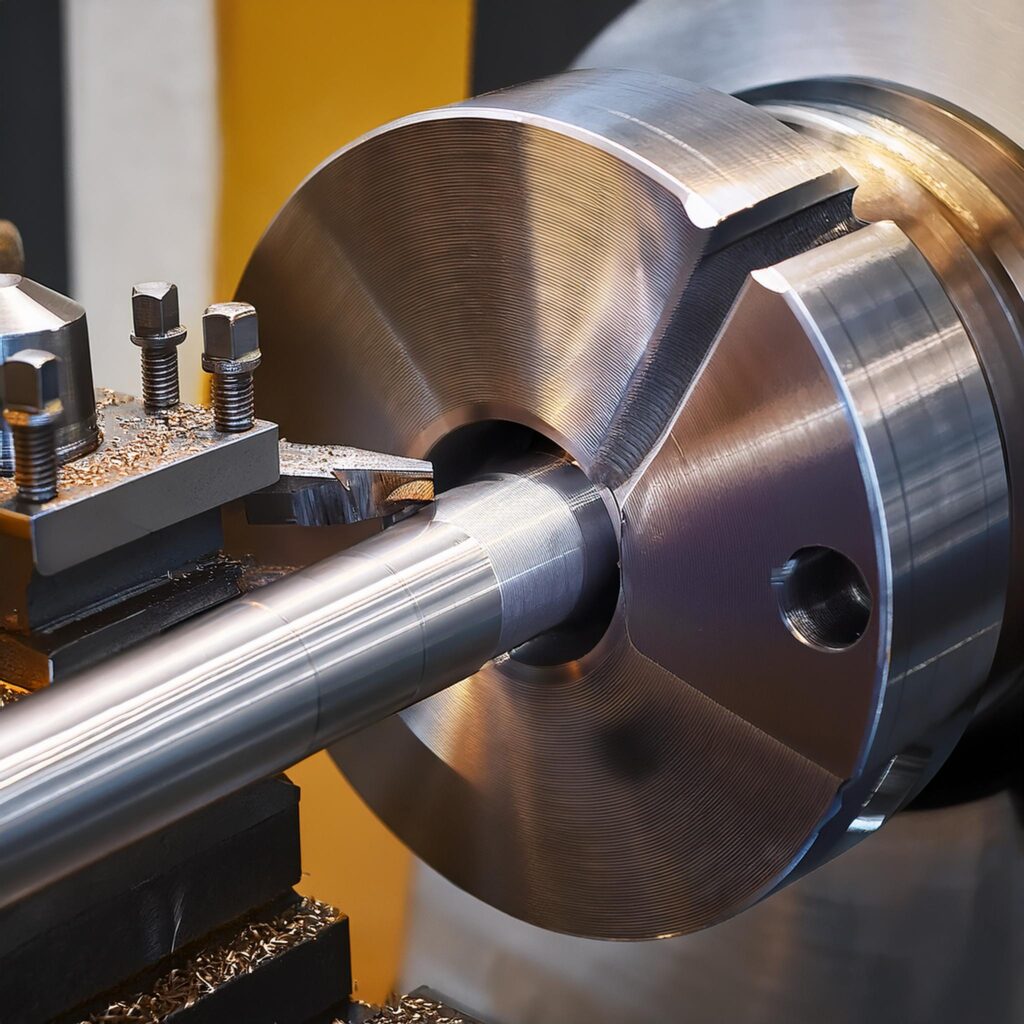
Stay Sharp, Stay Productive
Choosing the right combination of insert material and coating is essential for efficiency, tool longevity, and precision in machining. Whether you’re cutting steel, aluminum, or composites, there’s a perfect insert out there for the job. Keep your tools sharp, and your projects even sharper.