What to Know About Tooling Insert Shapes, Uses, and Pros & Cons
Picking the right tooling insert for machining metal isn’t always easy—there are so many shapes, coatings, and materials to choose from. The wrong choice can lead to rough finishes, worn-out tools, or even scrapped parts. Tooling inserts are essential in machining, offering versatility and efficiency for various applications. The different types of inserts are classified from A- to W-type. Understanding different insert shapes, uses, advantages and disadvantages can help optimize machining performance. This guide breaks down some of the most commonly used insert types to help machine smarter and more efficiently.
Common Insert Shapes, Angles & Uses
1. Square Inserts (S-Type, 90º)
-
- Use: General-purpose machining
- Pros:
- Durable, multiple cutting edges (typically 8 if double-sided)
- Offers strong cutting edges for facing, milling and turning operations
- Used on a variety of materials
- Cons:
- Less effective for detailed cuts or complex geometries
- Sharper corners may be more prone to chipping, especially on harder materials.
- Generates long, stringing chips. Chip breaker designs may be necessary on inserts.
2. Triangular Inserts (T-Type, 60º)
-
- Use: Light to medium cutting applications. Also used for turning, facing, threading or profiling.
- Pros:
- Three cutting edges per side, good for precision work
- Tooling symmetry offers good balance and precision during machining
- Offers better chip evacuation than square inserts
- Cons: Less durable than square inserts.
3. Round Inserts (R-Type, 0º Effective Cutting Angle)
-
- Use: Heavy cuts, roughing, contouring, and finishing
- Pros:
- Excellent strength and heat resistance
- Smooth cutting action for curved or complex surfaces
- Lack of sharp corners reduces the likelihood of chipping and longer tool life
- Cons:
- Higher radial cutting forces
- Requires more horsepower
- Requires increased rigidity
- Poor performance in straight cuts
- Broad cutting engagement leads to deflection on slender or less rigid parts
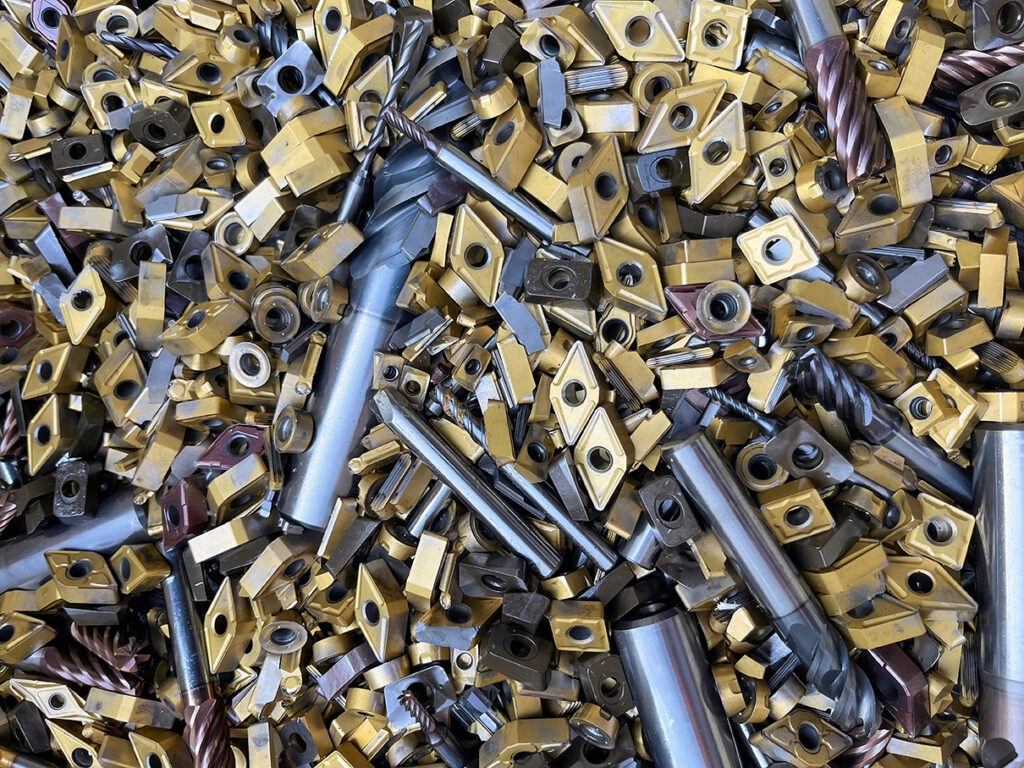
Industrial cutting tools inserts used to cut metals usually made from tungsten.
4. Rhombic-, Trigonal-, & Diamond-Shaped Inserts (D-Type 55º, C-Type 80º, V-Type 35º, and W-Type 80º):
-
- Use: Finishing and semi-finishing
- Pros:
- Ideal for fine detail work and smooth finishes
- Works well for tight corners and small features
- Cuts hard-to-machine materials like hardened steels, aluminum, titanium and composites
- Cons:
- Fewer cutting edges, less durable for heavy cuts
- Small contact areas create weakness at the tip
- Less suitable for aggressive roughing or high-feed machining
- Not great for interrupted cuts, square shoulders or straight-facing cuts
Choosing the Right Insert
Selecting an insert depends on the machined material, cutting speed, surface finish requirements, and tool life expectations. Choosing the right tooling insert doesn’t have to be a guessing game. Knowing the differences in shapes, angles, and applications, you can confidently pick the best insert for the job. With the right knowledge, you’ll get better finishes, longer tool life, and smoother machining every time.