3 Tips for Hard Turning on Your LeBlond Lathe
Turning hardened metals on a lathe takes additional care than turning standard metals. Taking the proper care while machining hard metals will reduce scrap, improve production, minimize finishing, and decrease maintenance and downtime.
What’s the difference between hardened and standard metals?
Hardened steel, titanium, heat resistant nickel alloys and other alloys can present difficulties when machining these materials. Common materials include: Inconel, Hastelloy, Stellite and other metal alloys. When cutting these materials, it is best to have a small length-to-diameter (L/D) ratio. Making sure the cutting process is flawless is vital since these harder metals are generally more expensive.
1. Considerations for Optimal Output
Your machine needs to have sufficient rigidity for hard turning applications. Keeping your lathe maintained and in excellent working condition will provide sufficient rigidity and tighter tolerances. Additionally, proper part support and close proximity to the turret will help minimize overhangs, extensions and shims that potentially impact rigidity.
2. Avoid the “White Layer”
The “white layer” is a very thin shell that forms on a part that is harder than the underlying layer. Resulting from dull inserts imparting too much heat on the metal, this can create part failure over time. When hard turning, it is important to perform random part tests to determine when the inserts become dull.
3. Boring is Exciting
High cutting pressures create added forces to the boring bar. Reduce pressure by using the appropriate insert angle, either 35-degree or 55-degree inserts with a small nose radius. Set your tooling on-center or slightly above part center for best results.
For more details about the best operation of your lathe for hard turning, consult your manual or contact a LeBlond representative for best results.
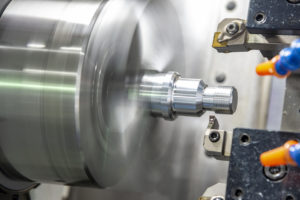
Lathe machine tooling.
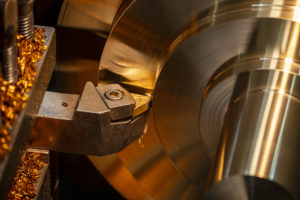
Lathe machine finishing process cuts brass shaft material. The metalworking process by turning machine.